
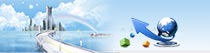
-
廣東啟綠環(huán)保工程設備有限公司
地址:廣東省東莞市塘廈鎮(zhèn)大坪社區(qū)上沿路2號
電話:0769-82853990手機:13712725152
傳真:0769-86346794
E-mail:qlhb88@163.com

軌道車輛涂裝VOCs廢氣治理技術的探討
編輯:啟綠環(huán)保 瀏覽: 時間:2019-04-17
近年來,軌道交通由于其快速、方便,并有效緩解城市交通壓力的特點,得到了快速發(fā)展。但目前我國軌道交通車輛涂裝還是以溶劑型涂料為主,隨著需求量的不斷增加,相應生產涂裝過程帶來的環(huán)境問題也引起了越來越多的關注,隨著國家對大氣污染防治的要求越來越嚴格,對軌道車輛涂裝噴漆室、烘干室廢氣排放的治理迫在眉睫。
一、軌道交通車輛制造中產生的涂裝廢氣特征
軌道交通車輛涂裝涂層包括防銹底漆、膩子、中涂漆和面漆,車輛內表面和底架下表面噴涂阻尼降噪涂料,部分列車底部噴涂防火涂料,目前涂裝主要采用的仍是溶劑型涂料。其中,涂料中的溶劑組分又以苯系物(甲苯、二甲苯較多) 、酯、醇、醚、酮為主,一般的涂料中有機溶劑占比為40%~60%。在噴涂工序,車輛車體每次完成一個涂層的噴涂后,都將進入噴漆室和烘干室,噴漆室和烘干室的VOCs產生量比例大約為5∶1~6∶1。
噴漆室廢氣主要污染物為未附著至工件表面的漆霧和工件表面涂料揮發(fā)出來的VOCs。為保證噴涂后工件的表面質量,噴漆室的氣流要參考我國相關設計標準,噴漆室通常采用上進下排的氣流組織方式,噴涂作業(yè)區(qū)空載風速不小于0.35m/s,有載時風速不低于0.5m/s。溫度條件為18~28 ℃。因此,噴漆室廢氣的特點是風量大、VOCs濃度低(大約為100~500mg/m3) ,且含一定的霧滴(其中漆霧不超過1mg/m3) 。
烘干室由于要保持一定的溫度,所以廢氣的風量不大,其組分與涂料中溶劑的組分基本一致(醇類、酯類、醚類、酮類、苯系物等) ,由于烘干室溫度相對較高,所以溶劑會在此工序中大量揮發(fā)出來,VOCs濃度一般在2500mg/m3左右,產生的廢氣為VOCs中等濃度、高溫型廢氣。
二、軌道交通車輛噴涂VOCs廢氣治理方案的選擇
車輛噴涂車間生產一般都是噴漆室和烘干室同時工作,雖然烘干室廢氣的濃度和溫度都較高,但是由于烘干室的風量較小(約為噴漆室的1/8~ 1/12) ,因此車輛噴涂車間產生的VOCs廢氣一般采用2個工段的廢氣經混合后集中處理,且廢氣特性基本屬于低溫、低濃度、大氣量、易吸附的VOCs廢氣;谲囕v涂裝生產產生的VOCs廢氣特征和目前我國較高的排放標準要求,如北京地區(qū)工業(yè)涂裝廢氣排放標準要求非甲烷總烴≤50mg/m3,總VOCs處理效率≥90%。綜合該治理系統(tǒng)的一次性投資、長期運行費用、環(huán)保達標排放等性能,車輛涂裝廢氣治理較為合理的處理技術為“廢氣的吸附濃縮凈化+脫附廢氣的高溫熱氧化”組合治理方案。
2.1吸附濃縮方案及其吸附劑的選擇
廢氣的濃度一般采用質量-標態(tài)下體積濃度(C)表示,按式(1) 計算:
C = m/Q 式(1)
式中: C—標準狀態(tài)下廢氣中VOCs的質量濃度,單位為mg/Nm3 ; m—廢氣中污染物的總質量,單位為mg; Q—廢氣的總風量,單位為標態(tài)下體積Nm3。
吸附濃縮使用的吸附劑一般有分子篩和活性炭2種,即將大風量低濃度的廢氣,吸附后實現(xiàn)達標排放,動態(tài)吸附飽和的區(qū)域,經再生氣再生,氣量降低若干倍,但再生氣中污染物濃度則增加若干倍(污染物遵循總質量m不變,實際受濃縮介質影響,會略微降低) ,從而實現(xiàn)系統(tǒng)處理能耗合理的目標。表1為分子篩和活性炭的性能對比。
表2 是某活性炭設備廠的活性炭在某噴涂工廠的實際應用數(shù)據,記錄數(shù)據的時間為每次完成脫附再生后和下一次脫附再生前,脫附周期為7d。
表3 是某沸石分子篩設備廠的沸石分子篩在某噴涂工廠的實際應用數(shù)據,由于其吸附和脫附同時進行,為保證數(shù)據的可對比性,記錄數(shù)據的周期也為7d。
從表2和表3可以看出,活性炭的吸附能力較分子篩強,但隨著使用時間和再生次數(shù)的增加,活性炭設備的吸附能力會明顯下降。活性炭雖然在脫附再生后處理效率可以有效提高,但是在7d的運行周期內下降較快,很可能在最后幾天出現(xiàn)不達標的情況,并且即使進行再生脫附,吸附效率也明顯下降,一般在300d左右就必須更換。因此,為保證穩(wěn)定的吸附處理效率,噴涂行業(yè)VOCs廢氣治理常用的吸附劑以沸石分子篩為主,同時疏水性改性沸石分子篩的應用進一步增加了其使用價值,濃縮工藝則以轉輪吸附濃縮工藝為主。
2.2高濃度再生廢氣治理方案的選擇
高濃度VOCs廢氣的治理方案通常為燃燒法或熱氧化法。目前主流燃燒方案有催化氧化(CO) 、蓄熱熱氧化(RTO) 和蓄熱催化氧化(RCO) ,3種主流方案的性能比較見表4。
從表4可以看出,CO的特點是工作溫度低,啟動時間短,比較適合間斷型生產工況,但是由于其使用催化劑,所以廢氣中必須控制會使催化劑中毒的成分。RTO的特點是工作溫度高,熱回收效率高,因為內部沒有催化劑,不會出現(xiàn)催化劑中毒的風險,所以適用范圍很廣,只要沒有強腐蝕性的氣體一般都可使用,但因為啟動時間較長,所以在間斷型生產的工況,需要長時間的保溫運行,燃料的消耗量較高。RCO結構與RTO相似,但也需要催化劑,因此,在涂裝VOCs廢氣的治理中少有應用。
軌道交通車輛噴涂的工況,一般情況下每天噴漆車間工作8h,屬于間斷型生產工況,所以催化氧化(CO) 是車輛涂裝生產中處理VOCs廢氣的優(yōu)選燃燒方案,如果廢氣成分中含有過多不適合組分的催化劑,且無法通過預處理消除時,則RTO是優(yōu)選的燃燒方案。
三、沸石轉輪濃縮+催化氧化(CO)系統(tǒng)
在車輛涂裝廢氣治理中的應用沸石轉輪濃縮+催化氧化(CO)系統(tǒng)主要由3個子系統(tǒng)組成,即廢氣的除濕和預過濾子系統(tǒng)、沸石轉輪濃縮子系統(tǒng)和催化氧化(CO)子系統(tǒng)。
3.1廢氣的除濕、預過濾處理子系統(tǒng)
高濕度廢氣對于沸石轉輪的吸附效率有著直接的影響。根據實際生產中的應用和多次試驗,廢氣的相對濕度低于80%時,沸石轉輪對VOCs的吸附效率可穩(wěn)定保持在90%以上,但當廢氣相對濕度大于90%時,對于某些VOCs 組分,沸石轉輪的吸附效率下降至80%左右。
若使用水性涂料,廢氣中實際相對濕度可能過高,因此,為保證廢氣中相對濕度低于80%,可將廢氣溫度提高從而降低廢氣的相對濕度。通常車輛涂裝VOCs廢氣處理系統(tǒng),入口廢氣溫度約30℃,如果入口溫度提高約2℃,大約可使入口廢氣的相對濕度降低15%。因此,即使車間廢氣的相對濕度達到100%,進入轉輪時的相對濕度也可降低至85%以下,但在實際的工業(yè)化應用中,宜將進入沸石轉輪的廢氣入口溫度提高至較車間混合廢氣溫度高3℃以上較為安全可靠。
其次,由于車輛涂裝廢氣中含有少量漆霧等顆粒雜質,為避免影響轉輪的吸附效率,通常預過濾采用初、中、高效組合過濾技術用于除顆粒雜質,但預過濾設計應盡量減少中、高效過濾器的更換頻次,以降低設備的運行成本。
3.2沸石轉輪濃縮子系統(tǒng)
轉輪是沸石轉輪濃縮子系統(tǒng)的核心部件,也是將低濃度VOCs濃縮的關鍵設備,它通常由疏水性沸石分子篩與陶瓷纖維加工成波紋狀膜片,再卷制成蜂巢狀的輪盤結構,并在輪盤的中央安裝旋轉軸承。耐腐蝕、耐高溫的氣體密封墊安裝在轉輪的外部框架結構上。通常轉輪隔離成3 個區(qū)域,即吸附區(qū)、脫附區(qū)和冷卻區(qū),轉輪速度通常以3~6r/h持續(xù)緩慢旋轉。
沸石轉輪濃縮子系統(tǒng)另一核心部分為再生氣加熱及其熱交換系統(tǒng),以及風機系統(tǒng)、自動控制系統(tǒng)等。目前全世界的轉輪廠家能夠提供的最大型號的單只沸石轉輪,最大可以處理200000m3/h風量的廢氣,根據處理廢氣的組分和濃度,能夠將廢氣中的VOCs濃度提高5~20倍。
沸石轉輪的目的是保證進入轉輪的超標VOCs廢氣經過轉輪吸附區(qū)吸附凈化后可直接排放至大氣中,被去除的原有VOCs成分被截留吸附在沸石分子篩內部,當轉輪上吸附有大量VOCs的片區(qū)旋轉至脫附區(qū)時,一臺小風量的脫附風機將180~240 ℃左右高溫氣體吹入轉輪中,并將其中吸附的VOCs脫附出來,此時便實現(xiàn)了廢氣的濃縮。脫附后的轉輪由于溫度較高,此時不具有較高的吸附性能,所以先進入冷卻區(qū),經冷卻氣體吹掃降溫,使其恢復吸附能力,而后再旋轉至吸附區(qū),重新開始下一輪的工作。每個區(qū)域都保持氣密。這樣轉輪的每個部分均可以連續(xù)地從吸附區(qū)旋轉到脫附區(qū),然后旋轉到冷卻區(qū),最后又旋轉回吸附區(qū)完成一圈的旋轉。
3.3催化氧化(CO) 子系統(tǒng)
催化氧化(CO)子系統(tǒng)通常由燃燒器或加熱器、貴金屬催化劑、閥組及安全報警裝置組成。催化氧化(CO)為無火焰燃燒技術,涂裝廢氣處理系統(tǒng)常見的催化氧化溫度在300~350 ℃之間,也可以高達600℃,處理效率可以達到99.5%以上,且無NOx產生。
催化氧化(CO)能夠將熱力燃燒不適合處理的低濃度VOCs,在不補給或少補給輔助熱量的情況下,將其氧化為無毒無害的CO2和H2O,從而節(jié)約大量的能源。圖1中顯示了一些常見的有機廢氣在Pt-Pd催化劑作用下,氧化溫度與處理效率的關系。
四、沸石轉輪濃縮+催化氧化系統(tǒng)的技術特點
(1) 對于大風量、低濃度的VOCs廢氣,具有較穩(wěn)定的凈化效率,通常該系統(tǒng)VOCs的處理效率可高達95%以上。
(2) 沸石轉輪由無機氧化物組成,自身不可燃,安全度高。
(3) 沸石轉輪可以承受300 ℃以上的脫附溫度,對于高沸點的VOCs也能夠有效處理。熱穩(wěn)定性極高,可以通過反復加熱脫附來實現(xiàn)再生,使用壽命高于40000h。
(4) 整個系統(tǒng)每次啟動時間小于1h,對于軌道車輛噴涂行業(yè)非連續(xù)運行的工況來說,系統(tǒng)啟/?欤\行靈活,可節(jié)約大量運行能耗。
五、沸石轉輪濃縮-催化氧化系統(tǒng)應用實例分析
以軌道車輛噴涂車間的2個噴漆房和3個烘干房涂裝廢氣治理為例,對其廢氣處理系統(tǒng)進行實例分析。本案例的噴涂車間每天工作約8h,其中有效工作時間不小于6h。
5.1系統(tǒng)設計參數(shù)的計算
5.1.1風量計算
按照每間噴漆房排風量100000m3/h,每間烘干房排風量以10000m3/h來計算,此系統(tǒng)的處理總風量為230000m3/h。
5.1.2廢氣濃度及組分檢測
此噴涂車間涂料以水性涂料為主,廢氣中VOCs濃度為80~250mg/m3,污染物主要成分為乙二醇丁醚、三甲苯、乙酸丁酯與少量溶劑油。
5.2系統(tǒng)工藝設計
考慮到廢氣濃度的波動性和廢氣排放穩(wěn)定達標性,系統(tǒng)設計預留20%的余量。則本項目廢氣總風量為276000m3/h,超過了單臺轉輪200000m3/h的最大處理風量,故選用2套3550mm×400mm沸石轉輪,換輪的處理氣量138000m3/h,濃縮比20∶1; 濃縮后廢氣進入一臺處理能力為13800m3/h的催化氧化子系統(tǒng)。系統(tǒng)通過二級換熱回收氧化爐熱能,確保能源利用的經濟性。處理流程見圖2。
5.3系統(tǒng)的處理效果
經檢測,此套系統(tǒng)對于風量276 000m3/h,濃度80~250mg/m3,主要成分為乙二醇丁醚、三甲苯、乙酸丁酯與少量溶劑油的VOCs,處理效率不低于90%,非甲烷總烴排放濃度可穩(wěn)定低于30mg/m3,基本滿足現(xiàn)有國標及地標的排放標準。
六、結語
沸石轉輪濃縮+催化氧化(CO) 處理方案,是車輛涂裝VOCs廢氣治理的合理工藝,處理工藝系統(tǒng)安全、去除率高、穩(wěn)定性高、運行費用合理可行。因此,沸石濃縮轉輪+催化氧化(CO) 技術是現(xiàn)有技術條件下對于非連續(xù)工況,處理大風量、低濃度VOCs廢氣的最佳選擇,在軌道車輛涂裝廢氣治理中的應用將會越來越廣泛。
來源:涂料工業(yè)
下一篇:有機廢氣活性炭吸脫附催化燃燒裝置

