
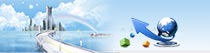
-
廣東啟綠環(huán)保工程設備有限公司
地址:廣東省東莞市塘廈鎮(zhèn)大坪社區(qū)上沿路2號
電話:0769-82853990手機:13712725152
傳真:0769-86346794
E-mail:qlhb88@163.com

RTO技術在丁辛醇裝置化工異味治理中的應用
編輯:啟綠環(huán)保 瀏覽: 時間:2019-03-04
丁辛醇裝置采用Davy/Dow低壓銠催化劑羰基合成工藝,以羰基合成氣和丙烯為原料生產丁辛醇。該裝置分為原料凈化、羰基合成、蒸發(fā)、丁分離、丁醛縮合、辛烯醛加氫、丁醛加氫、丁辛醇精餾等8個工序;ぎ愇秮碓礊橛薪M織排放度氣和無組織排放度氣兩部分,通過技術改造、回收利用、生物除臭等措施實現(xiàn)了有組織廢氣集中處理,無組織廢氣經密閉回收集中處理,化工異味綜合整治,取得了明顯效果田。但也存在生物除臭裝置QBF運行不穩(wěn)、有機廢氣去除效率低、運行成本高,操作難度大等問題,導致VOC、排放達不到新的環(huán)保標準。因此尋找開發(fā)一種操作簡單、效率高、運行成本低、運行穩(wěn)定的化工異味治理技術顯得尤為重要。
一、丁辛醇裝置廢氣未源及VOCs含量
丁辛醇裝羅廢氣分別來自儲罐、構筑物及生產設備。儲罐廢氣指儲罐在物料裝填或內部壓力上升時通過呼吸閥排放的醇、醛類揮發(fā)性有機物,現(xiàn)有丁醛儲罐、丁醇儲罐、辛醇儲鑵共計22臺。構筑物廢氣來自裝置污水池及廢液池。生產設備廢氣來自辛醇精餾系統(tǒng)真空發(fā)生器3641和J202排放的廢氣。各來源點廢氣組成、濃度變化較大,特別是儲罐受物料飽和蒸汽壓、進料速、液位、溫度、氮封等因素影響較大,VOCs濃度以現(xiàn)場實測與經驗計算相結合,廢氣量根據儲罐進料量確定。廢氣來源見表1。
二、RTO蓄熱氧化技術簡介
常用的工藝廢氣處理技術有冷凝法、吸附法、吸收法、生物處理技術、催化氧化法、焚燒法、低溫等離子廢氣處理技術、高溫氧化技術等。高溫氧化技術分為蓄熱式氧化爐( Regener-ative Thermal Oxidizer,簡稱RTO)、蓄熱式催化爐(RCO)、催化氧化爐(CTO)、直燃氧化爐(TO)等RTO蓄熱氧化技術是利用氧化過程將VOC廢氣轉換成無害的CO2與H20,同時利用陶瓷材質做成的蓄熱材料,利用其蓄熱及放熱原理設計的高溫氧化技術。其原理是把有機廢氣加熱到800℃以上,使廢氣中的VOCs在氧化室中氧化分解成CO2與H12O。氧化產生的高溫氣體流經特制的陶瓷蓄熱體,使陶瓷體溫而“蓄熱”,此“蓄熱”用于預熱后續(xù)進入的有機廢氣,從而節(jié)省廢氣升溫的燃料消耗。蓄熱式氧化爐分兩床式、三床式、旋翼式等型式,RTO高溫氧化技術可以針對廢氣濃度低、波動大、含有各種高毒性、惡臭成分的度氣處理,尤其適用于石化行業(yè)的VOCs廢氣處理。反應原理如下:
三、丁醇裝置RTO設備
3.1流程簡圖
RTO設施流程見圖1。
3.2工藝簡介
根據丁辛醇裝置廢氣組成、濃度變化較大的特點,從處理條件、授資費用、運行成本和運行穩(wěn)定性及處理效率等綜合比選,丁辛醇裝置廢氣治理適合選用單箱旋翼式RTO技術。
RTO設施包括廢氣收集和廢氣處理兩部分,主要包括蓄熱氧化室、風機等。丁辛醇裝置構筑物經風機FN8101引入混合箱、生產設備產生的廢氣經集氣單收集后在其收集總管道上加入稀釋風進一步降低VOCs濃度后經風機FN8102引入混合箱、儲罐產生有機廢氣通過集氣罩收集后在其收集總管道上加入稀釋風進一步降低VOCs濃度后經風機FN8103引入混合箱,混合后廢氣由排風風機FN8104排出,經水封裝置由主風機FN8105送出,經底部旋轉閥進入蓄熱氧化室中,氧化室內裝蜂窩蓄熱陶資,在800~840℃溫度下,將廢氣中的VOCs氧化成CO2、H2O,然后進高25m煙囪排至大氣。氧化室內有8個進氣通道順序切換使用, 由旋轉閥旋轉頏率控制每個氣道的切換周期。如RTO出現(xiàn)故障或VOCs濃度異常時廢氣將通過備用活性炭吸附塔進行處理后排入大氣儲罐呼吸閥出口廢氣輸送管和呼吸閥連接方式由直聯(lián)改為集氣罩方式,收集時同時吸入足夠的空氣,降低VOCs濃度。集氣單后端帶有止回閥,可防止氣體回流,止回閥后端帶有手動調節(jié)閥,根據與排風機的距離、管道壓力損失的不同,適當調節(jié),實現(xiàn)各儲罐的排放平衡。儲罐口増加且火器,防止串火。
3.3RTO關鍵參數確定及安全環(huán)保措施
3.3.1 RTO處理風量確定由于廢氣中含有H2、CH4、丁醛等易燃易爆物質,廢氣收集必須保證在最大VOCs濃度下不超過爆炸下限(LEL),根據安全要求,控制在20%LEL以下。根據每個呼吸閥提供的排風量容量,總排風量為2650m3/h,加100%的稀釋風余量,儲罐區(qū)的總排風量為5000m3/h。生產設備真空發(fā)生器3641及J202的廢氣含有氫氣、甲烷等易燃氣體和VOCs,極端工況下混合氣體的爆炸下限為3.7%,稀釋風量定為5000m3/h,將其稀釋到安全濃度以下后與其他廢氣一同處理。構筑物廢氣由單獨的風機輸送到處理設備區(qū),風量按260m3/h設計,濃度忽略不計。合計總風量為10260m'/h,考慮處理冗余量,RTO設施設計處理風量為15000m3/h。風量及VOCs含量見表2(均未考慮總管稀釋風)。
3.3.2エ藝運行參數確定
a)RTO燃燒室溫度控制在800~840℃。
b)生產設備排風風機102入ロ壓カ-500Pa,儲罐廢氣排風風機103入ロ壓力-3000Pa,調整依據是保證生產設備集氣單及稀釋風管道、儲集氣罩維持微負壓,既要滿足廢氣從排放源順利地排出又要盡可能減少排放量。
c)主風機入ロ壓力-1000Pa,由變頻電機驅動,根據排放設備的排放風量變化產生,自動調節(jié)轉速,適應排放工況。
d)爆炸下限聯(lián)鎖值設定為可燃氣爆炸下限的20%。
3.3.3安全保護措施
由于廢氣中含有H2、CH4丁醛等易燃易爆物質,爆炸下限低,爆炸極限范圍大,加入稀釋風后,極易進入爆炸范圍,因此借鑒國外同類RTO設施閃爆事故的教訓,設計安全保護措施如下:
a)風量設定滿足可燃氣體最大運行濃度低于爆限下限的20%。
b)風機內防爆,防止VOCs濃度超過爆炸下限時風機發(fā)生爆炸。
c)管道采用防靜電設計,防止氣體流動時發(fā)生靜電火花。
d)每一個廢氣排放設備的排氣管道均帶有阻火器,防止外部的火焰波及到設備。
e)總管道裝有溫度傳感器,如有異常高溫,隔離后端設備進行排空,防止廢氣發(fā)生端的火焰波及到RTO和備用吸附床。
f)廢氣和RTO設備之間裝有帶爆破片的水封裝置,防止RTO發(fā)生意外時火焰?zhèn)鞑サ角岸?
g)采用集氣罩收果氣,以高高度氣管道和儲罐,同時提供充足的稀釋風。
h)主管道帶有爆炸下限傳感器,實時提供度氣濃度(爆炸下限比例),并提供報警和聯(lián)鎖功能。
i)安全控制點采用SI3安全等級傳感器,并通過安全繼電器直接(不通過程序)啟動帶有SIL3安全等級的執(zhí)行裝置(如電磁閥)。
j)RTO入口帶有爆破片,在發(fā)生爆炸時將能量安全地擴散,防止人員傷亡和設備破損。
k)RTO的燃燒器輸出由DCS自動控制,燃燒器閥組帶有可燃氣體探器,可監(jiān)視燃料的泄漏.出現(xiàn)異常,提供報警信號和聯(lián)鎖功能。
l)三路中有一路風機發(fā)生故障時,及時切換至原生物除臭裝置QBF運行。
m)當主風機故障時,RTO停車,三路有機氣體及時切至原生物除臭裝置QBF。
四、運行效果
丁辛醇裝置RTO設施于2017年5月開始建設施工,于2017年9月11日點火試運行,運行期間生產穩(wěn)定,氧化室控制溫度815~835℃,取樣煩次1次/h,VOCs濃度取24h平均值,運行結果
從表3看出,入口VOCs濃度在551~1440mg/m3時出口濃度在22~70mg/m2之間,滿足CB31571-2015《石油化學工業(yè)污染物排放標準》即非甲烷總烴濃度≤120mg/m的要求。
五、建議
a)丁辛醇裝置RTO廢氣處理設施在正常工況下能達到非甲烷總烴濃度≤120mg/m的要求,但有時不能達到非甲烷總烴去除效摔≥97%的要求,建議進一步優(yōu)化工藝指標,増加RTO入口旋轉閥反吹風機,將旋轉閥切換時漏入出氣口廢氣反吹回氧化爐,提高廢氣處理效率。
b)運行過程中出現(xiàn)生產設備J202廢氣投用后經常引起廢氣爆炸下限LEL8101-8103高聯(lián)鎖動作發(fā)生,建議進一步優(yōu)化FN1O2風量及總管稀釋風量,降低VOCs濃度。
來源:《安全、健康和環(huán)境》
上一篇:濾筒除塵器的6項日常檢查內容
下一篇:惡臭廢氣及有機廢氣的處理工藝

